Some key Technical issues in QS 9000(automotive standards) and TS16949 is given below
The key differences between QS-9000 and ISO/TS 16949:
The key differences between QS-9000 and ISO/TS 16949 relate to the aspects of customer and employee satisfaction.
Customer Satisfaction:
Both QS-9000 and ISO/TS 16949:1999 require a documented process for measuring customer satisfaction.
This includes the documentation of trends and the comparison of benchmark data.ISO/TS 16949:2002, additionally specifies that companies should:
* Determine a method for monitoring customer perception as to whether requirements have been met,
* evaluate data continuously,
* demonstrate compliance with customer requirements & efficiency of process.
Employee motivation, Empowerment & Satisfaction QS-9000 makes no reference to employee motivation whilst TS 16949:1999 requires that companies develop a process for the measurement of employee satisfaction.
ISO/TS 16949:2002 additionally specifies that organizations:
* have a process for measuring satisfaction to achieve quality objectives & make continual improvements,
* promote quality awareness at all levels,
* make personnel aware of the relevance of their activities.
|
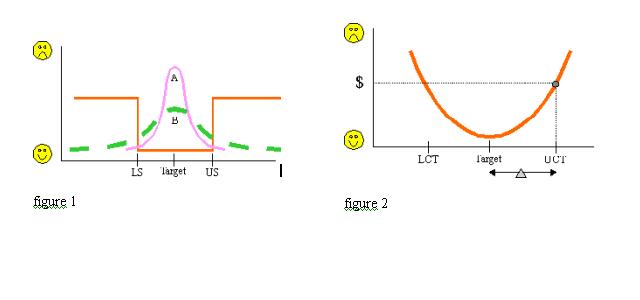 |
Taguchi's Approach to Quality Engineering:
Introduction Robust design (RD) is an important methodology for improving product manufacturability and life, and for increasing manufacturing process stability and yield. Since its introduction to U.S. industry in 1980, Taguchi's approach to quality engineering and robust design has received much attention from designers, manufacturers, statisticians, and quality professionals.
Essentially, the central idea in robust design is that variations in a product's performance can inevitably result in poor quality and monetary losses during the product's life span. The sources of these variations can directly be classified into the two categories of controllable and uncontrollable or noise parameters. For instance, in a typical design application, factors such as geometric dimensions of a part can easily be controlled by designers.
Uncontrollable or noise factors such as environmental variables, product deterioration or manufacturing imperfections, on the other hand, are also sources of variations whose effects can not be eliminated. Therefore, RD's main function is to reduce a product's variation by reducing the sensitivity of the product to the sources of variation rather than by controlling these sources. In other words, RD reduces response variation by selecting appropriate settings for controllable parameters as to dampen the effects of hard-to-control noise variables. This is the crux of off-line quality control . Taguchi's Methodology for implementing robust design is essentially a four step procedure which can best be illustrated as follows:
For more details, you can now click on each of the following four options: * Formulate the problem * Plan the experiment * Analyze the results * Confirm the experiment
Taguchi's Loss Function
How to Measure Quality
Traditionally, quality is viewed as a step function as shown by the heavy line graph in the figure 1. A product is either good or bad. This view assumes a product is uniformly good between the specifications (LS the lower specification and US the upper specification). The vertical axis represents the degree of displeasure the customer has with the product's performance. Curves A and B represent the frequencies of performance of two designs during a certain time period. B has a higher fraction of "bad" performance and therefore is less desirable than A.
See figure 1 above
Sometimes traditional decision makers and those using Taguchi's loss function will make the same judgments. If organizations consider both the position of the average and the variance, and if the averages are equal and/or the variances are equal, then the traditional decision maker and one using Taguchi's loss function will make the same decision. However, the traditional decision-maker calculates the percent defective over time when both the average and variance are different.
See figure 2 above
Taguchi believes that the customer becomes increasingly dissatisfied as performance departs farther away from the target.
He suggests a quadratic curve to represent a customer's dissatisfaction with a product's performance. The quadratic curve is the first term when the first derivative of a Taylor Series expansion about the target is set equal to zero. The curve is centered on the target value, which provides the best performance in the eyes of the customer. Identifying the best value is not an easy task. Targets are sometimes the designer's best guess.
LCT represents lower consumer tolerance and UCT represents upper consumer tolerance. This is a customer- driven design rather than an engineers specification. Experts often define the consumer tolerance as the performance level where 50% of the consumers are dissatisfied. Your organization's particular circumstance will shape how you define consumer tolerance for a product.
The equation for the target-is-best loss function uses both the average and the variance for selecting the best design. The equation for average loss is:
|
|
|
|
|
|
|
|
|
|
|
|
|
|
|
|
|
|
|
|
|